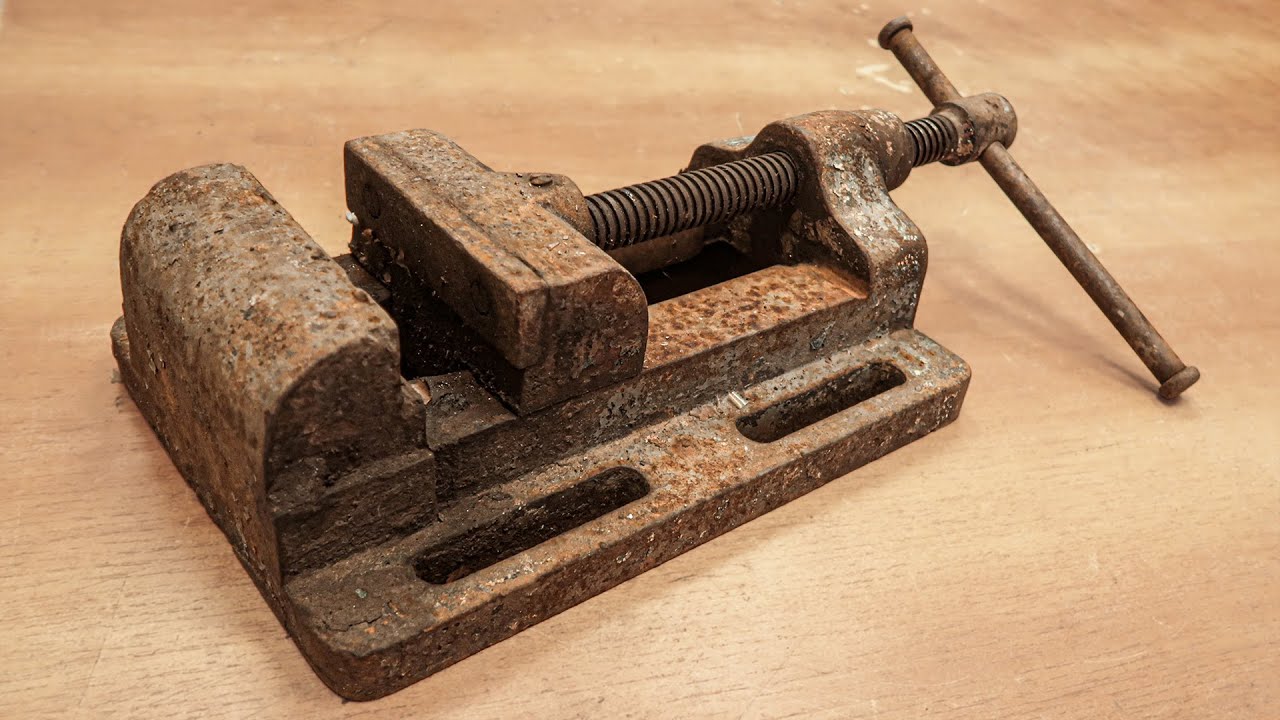
Here is a list some of the stuff I use for my projects:
It's affiliate marketing, so if you order something from here you'll help me making videos for free! Thank you!
Index of operation and materials:
2:15 One of the old jaw bolt was stuck. Since I knew I was going to make new jaws and I only had one of the original anyway I decided to cut it off.
3:24 Existing mounting holes preserved as I have been able (after much sturggle) to get stuck bolt out
3:47 Scrape off loose dust and grease
4:07 WD40 as tap lubrificant
4:15 Go over existing thread with tap to clean the threads and holes
4:40 For small parts the bench grinder / buffer with a steel wire wheel is the best
5:50 Spray degreaser
6:06 Grind off some big weld spots
6:30 Electrolysis: water and sodium carbonate solution, parts connected to negative side and steel sacrificial anodes to positive sice of a DC power supply (car battery charger). 2-3 hrs at 5amp.
7:00 Remove patina with steel wire brush in water
7:24 I could have left the vise in the electrolysis bath longer and skip this step, but I was in late!
7:41 a die grinder with a small steel wire bit is super handy for small places like this
8:20 Clean holes well with nitro solvent and alcohol
8:46 Two part filler (I notices chips tend to fall in holes like this if left open)
9:27 Grind flush with palm sander and low grit sandpaper
9:53 Old, thick, and worn out file
10:10 Cut required lenght with angle grinder and cut off disk
10:34 The file is hard, it snaps!
10:56 Annheal the file, hearing to 860 and letting to cool slowly
11:20 Difference between hard and annhealed file, hear the sound
11:50 Now the steel can be cut with the metal cutting bandsaw
12:24 Grind square with 2x72 belt grinder
11:52 Center puch
13:04 And drill holes
13:33 Now I can harden the steel by heating to critical and quenching in warm oil
14:05 And then temper for 2hr (jaws harness ended up between 50 and 55 Rockwell)
14:30 Making fasteners for the jaws out of hardware I have available, heads needed to be ground smaller on the 2x72 belt grinder
15:00 And also cut to lenght on the metal cutting bandsaw
15:47 Lead scwer was almost broken at the end, it has been repaired poorly so I went over with more welds
16:20 and ground new slot for the grub screw with die grinder and stone bit
17:58 Add a thin piece of copper sheat as spacer.
18:35 Grub screw replaced with new one
All parts are and will be keept well lubed up, I like this one raw steel!
Thanks a lot for watching, I hope you liked the video!
Suggestions and comments are welcome.
Leave a like and share to anyone who might be interested!
★Patreon★
★Website★
★Follow me★
Facebook ►
Twitter ►
Instagram ►
0 Comments